Entreprise:
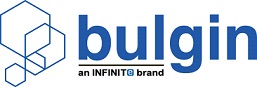
BULGIN TUNISIE
Secteur: électronique / électricité / énergie
Taille: Plus de 500 employés
Secteur: électronique / électricité / énergie
Taille: Plus de 500 employés
Bulgin, une société de conseil en connectivité mondiale, est largement reconnue comme l'un des principaux fabricants de connecteurs et de composants étanches à l'environnement. Avec plus de 95 ans d'expérience dans l'industrie, notre vision est de continuer à innover et à développer des produits et des services pour répondre aux besoins de notre clientèle mondiale sur une variété de marchés.
Description de l'annonce:
For it to be considered, please submit your resume in English.
Purpose of Role
The primary responsibility of the Customer Quality Engineer is to enhance customer satisfaction through analysis and
evaluation of customer feedback and internal performance data. In this role, you will serve as the central point of contact for
rapid resolution of customer quality issues and complaints.
Your responsibilities include coordinating the resolution of customer complaints, field failures (RMAs), and stock returns by
collaborating with cross-functional teams. utilising appropriate problem-solving tools to implement timely and effective
corrective actions, including stop ship, stop build, and product recalls. Prompt escalation of customer quality issues, stock
returns, or customer perception concerns is essential to ensure immediate resolution.
As Customer Quality Engineer, you will play a pivotal role in measuring and monitoring customer perception using data from
RMAs, customer complaints, surveys, customer-supplier scorecards, and internal leading performance indicators for customer
satisfaction. You will utilise this information to generate internal customer quality dashboards and external customer
scorecards.
Key Accountabilities.
The role will require to:
● Manage Customer Quality Issues, such as RMA, customer complaints
o Resolve effectively customer quality issues in a timely manner, utilising the appropriate problem-solving
techniques to provide appropriate solutions and update the required BMS documentation, such as Process
Flows, FMEAs, Control Plans, Work Instructions, etc., as per CSR/Business
● Lead customer resolution meetings and actions follow up
o Generate and communicate 8D reports
● Coordinate recall and customer notification to ensure customer is notified immediately when nonconforming
product has been shipped Coordinate stock returns
o Coordinate implementation of actions resulting from the customer perception and internal customer quality
issues
o Communicate and mitigate the risks from the customer quality issues
● Ensure lessons learnt from the customer quality issues are conducted and fed back to the product development
teams and projects
● Drive the business with the customer focus by setting up and maintaining the customer quality dashboard
● Manage Customer Perception and Audits
● Assess and improve Bulgin processes
● Monitor customer quality KPIs to identify opportunities for improvement, communicate customers’ feedback
to cross-functional teams and lead improvement implementation
● Ensure customer related processes are effective, propose and lead required continuous improvement
initiatives implementation to improve customer satisfaction, i.e.
● The individual who is customer-focussed,
punctual, demonstrates good attention to detail. The individual with a strong background in implementing and utilising
advanced quality tools with statistical methodologies. A quality professional with extensive knowledge and expertise gained
from working in a manufacturing environment, preferably within the automotive or an equivalent demanding industry.
Availability to a flexible working to address Customer Quality Issues to accommodate different time zones and to travel
internationally is essential.
Qualifications and Experience
Essentials:
• Engineering diploma or Quality Management specialist with equivalent degree
• Significant engineering experience in resolving customer issues, enhancing customer satisfaction, measuring and
monitoring customer perception
• Significant quality assurance experience, including quality systems, standards, metrics, and tools
• Proven ability to act as Subject Matter Expert related to problem solving and the use of the core quality and lean
tools, such as 8D, PPAP, FMEA, Control Plans, SPC, TPM, DoE, Capability Studies, etc.
• Strong organisational skills and ability to prioritise workflow to meet established time frames and schedules
• Effective communication skills and an attitude for successful collaboration within cross-functional teams
• Strong attention to detail and a proactive learning attitude
• Demonstrated knowledge of ISO 9001 Quality Management System Requirements
• Technical knowledge of reading drawings, geometric tolerances, measurement and testing equipment
• Proficient of software programs – Microsoft (MS) Word, MS PowerPoint, MS Excel, Minitab
Desirable:
• Demonstrated knowledge of IATF 16949 Quality Management System Requirements
• Working experience in automotive product, process and layered audits
• Completed Lean, Six Sigma certification
• Proficient of software programs – Qualipro, IFS, Cognidox
• Health and safety knowledge
• First aid fire fighter traine
For it to be considered, please submit your resume in English.